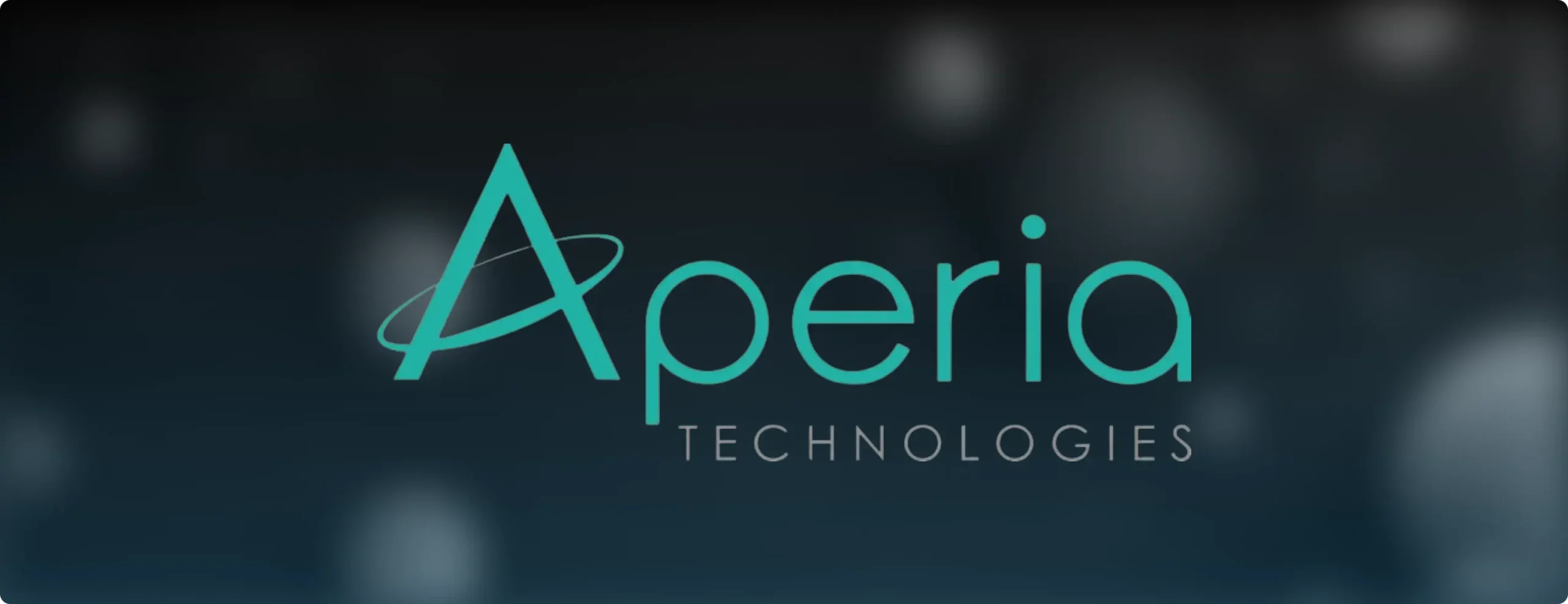
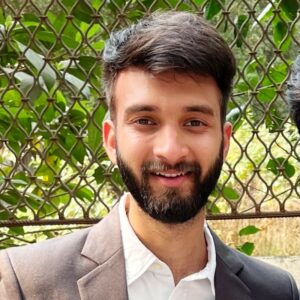
How Aperia Technology Achieved Data-Driven Operational Excellence with DronaHQ
Every day, across the sprawling network of commercial transportation, tires bear the weight of thousands of miles of journeys. While they may seem like simple rubber circles, their role is absolutely critical. You see, maintaining the right tire pressure isn’t just about keeping those wheels turning – it’s about keeping businesses moving. Imagine, for a moment, a single tire losing just a bit of air. Sounds harmless, right? Well, in this world of tight schedules and tight margins, that tiny loss can trigger a chain reaction of delays, increased expenses, and even safety hazards.
That’s where Aperia Technologies comes in, a leading tire inflation and management solutions provider. “Aperia Technologies is primarily a tire inflation company with a huge hand in tire management as well. So we aim to be a one-stop shop for tire inflation management for commercial fleets,” says Nicholas Vandehey, Production Engineer at Aperia Technologies.
Nicholas holds the position of Production Engineering Manager. In this role, Nicholas spearheads various engineering initiatives within the operations team. His primary focus involves managing the extensive data generated by their factories, meticulously integrating data sources from diverse test equipment.
The challenge: Managing complex data
Imagine you’re in charge of managing factory data, dealing with tons of information pouring in from various testing equipment around the world. It’s like having a vast library of valuable books, but without a proper catalog, it’s nearly impossible to find the right one when you need it. Nicholas recognized this challenge and decided it was time to transform their data management.
Now Aperia Technologies sought a frontend builder solution to address the complexities of their data management and operational needs.
Nicholas then decided to start using DronaHQ after looking out for other low-code tools in the market. The decision to select DronaHQ as its frontend builder was motivated by its pricing, the range of ready DBs and API connectors, and managing end users and native integration with Plotly for the charts.
“I knew I wanted a front end because it was going to make everybody’s life easier,” Nicholas says.
Building a dynamic frontend with DronaHQ
In their quest to optimize factory data handling and empower team members across departments, they found the perfect ally in DronaHQ. The platform allowed them to construct a robust and user-friendly frontend that simplified data access and reporting. It transformed processes like data retrieval and analysis into seamless tasks.
“We have data coming off of our machines, our raw data, and we need to be able to browse that through graphs and become accustomed to doing that in a certain way. Plotly is the perfect tool for executing that. DronaHQ had the native implementation, which is quite honestly maybe a little bit harder to execute, but it gave me all of the flexibility to plot data just the way I envisioned,” he says
With DronaHQ’s flexibility, Nicholas and his team were able to craft tailored solutions for their unique needs, all while ensuring scalability to accommodate the company’s evolving demands.
Here’s how they used DronaHQ and the problems they solved:
1. Data Management: Aperia Technologies had a significant challenge in managing their factory data and testing data. They needed to integrate data from various sources, including on-site and off-site test equipment, and ensure that this data was accessible and organized efficiently.
Solution: They used DronaHQ to create a custom application that served as a front-end interface for managing and browsing their manufacturing data. This application streamlined the process of accessing and analyzing factory data.
2. Integration with Third-Party Systems: Aperia Technologies wanted to ensure that their data could be integrated with third-party systems and products used by their customers.
Solution: They mentioned developing a product called “Halo Connect” within DronaHQ to achieve this goal. This product likely allowed them to integrate their tire data with various third-party systems used by their customers, making their data accessible through these systems.
3. Efficient Data Access for Non-Technical Users: Aperia Technologies faced a challenge where non-technical team members, including those in quality and manufacturing, needed access to complex data without extensive technical skills.
Solution: They used DronaHQ to build user-friendly front-end applications that enabled team members to access and analyze data without the need for programming skills. This improved efficiency and accessibility across different teams.
The results: Aperia Tech’s success story
Aperia Tech’s journey with DronaHQ has been transformative. They’ve evolved from wrestling with unwieldy spreadsheets and fragmented data to having a unified platform that empowers their teams. Nick and his team could bring their innovative ideas to life, and the results speak for themselves:
Enhanced Efficiency: Complex data operations that once took weeks now happen seamlessly.
Improved Accessibility: Team members with diverse technical backgrounds can now use data-driven insights in their work.
Future-Ready: Aperia Tech’s journey continues with plans to integrate ERP data and expand data connections and build custom tools not just for his team but across the organization.
Aperia Tech’s journey shows how using DronaHQ’s low-code platform can boost innovation and make operations smoother. It’s not just about making current processes simpler; it’s about finding new opportunities and getting more from your data.
Ready to transform your operations? Discover the power of DronaHQ today. Schedule a demo